Updated October 2021
Injection Molding of Soft Robots
By Dr. Michael Bell & Prof. Kaitlyn Becker, '21
Published in Advanced Material Technologies
10.1002/admt.202100605
We've pioneered a low-cost injection molding method to make low-volume soft robots and parts, and we are excited to share the processes, equipment, and examples of our work.
To date, injection molding has not been a practical manufacturing method for soft robots due to machine costs, large volumes of liquid silicones required, and the inability to change materials quickly between shots. Injection molds are typically machined from metals to allow for high pressure and clamping forces, which further limits the ability to rapidly prototype soft robots when molds could cost thousands of dollars. To circumvent these issues, we have pioneered a low-cost injection molding system and process. Here, we describe the apparatus, design process, economics, and workflow using standard SLA and polyjet 3D printers to rapidly iterate on soft robot designs.
Repeatable, Higher Resolution, and Faster Parts
Soft robots are primarily manufactured in low-volume laboratory settings, traditionally by mixing silicones by hand ($1s), turbine mixer ($10s), stand mixer ($100s), or planetary mixer ($10,000s). In industrial manufacturing of silicone products, liquid silicone injection molding is used to quickly and repeatably produce parts. These liquid silicone injection molding machines ($10,000s - $100,000s) are set up for mass manufacturing of one part, loaded with tens to hundreds of liters of one type of silicone, and do not allow for quick and easy replacement of molds or materials. The two desirable characteristics of these machines are their capacity for high pressure injection molding and the ability for continuous, in-line mixing. Mixing is accomplished in either a static mixer, which can contain dozens of speciality designed static elements to promote mixing as material passes through, or an active mixer which has a powered impeller to mix both materials as they pass.
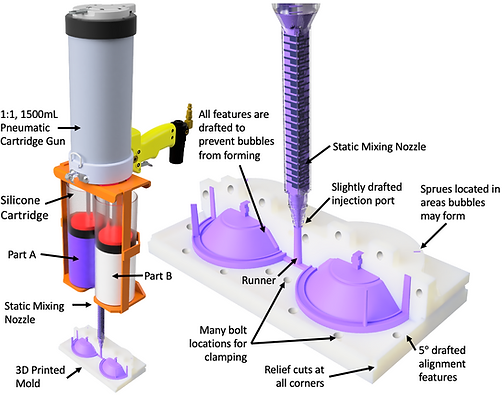
Build Your Own Injection Molding Setup

This google sheet contains the main components in the injection molding station.
The main items are:
- Cartridge Guns
- 80/20 Aluminum Framing
- McMaster hardware
- Scissor jack stand
The disposables are:
- Cartridges & pistons
- Mixing Nozzles
This is the BOM for the 80/20 table that was ordered:
This is the drawing for the HDPE tabletop that is manufactured by 80/20 (and part of the 80/20 quote):
The costs associated with molding a 50 ml silicone part, such as a PneuNet actuator, can be compared as seen in the table to the right. About one in five PneuNet-type actuators fail during casting, typically from bubbles immediately discovered or found during use. Although bubble defects can be repaired, we consider a 20% defect rate. Alternatively, for the same molds redesigned for injection molding, a defect rate of closer to 1% is achieved by eliminating bubbles and increasing the consistency of molding, in addition to greatly increasing the complexity of the part. From the table, injection molding has no cost advantage making a single part, however as the volumes increase to four or more parts, injection molding becomes less expensive. Overall, the per-part costs associated with injection molding is a few dollars, and is minor when taking into account the cost of the 3D printed mold and silicone material, which can run up to $140 for a similar part.
Mixing Quality - By Hand, Thinky, or Injection
Silicones are typically mixed with a centrifugal planetary mixer (such as a Thinky or FlackTek SpeedMixer), stand mixer, or by hand. To give reassurance that materials traditionally mixed in a centrifugal planetary mixer were equivalent to static mixing nozzles, tensile tests were performed according to ASTM D412 for three commonly used silicones, with six types of static mixing nozzles. The three silicone rubbers were also mixed by hand following the supplier recommendations, stirring for three minutes (with a wooden mixing stick from Smooth-On), scraping all edges during the mixing process, and degassing in a vacuum chamber at 29 in. Hg (736 Torr) for three minutes immediately after mixing. Material was cast into a sheet, and punched with an ASTM D412 Sample Cutting Die (Type C).
The mixing results for all materials showed no statistically significant difference between mixing methods, except a couple outliers. Hand mixing generally was equivalent to centrifugal planetary mixing. Static mixing nozzles generally performed equivalent or slightly better than hand or planetary mixing. Centrifugal planetary mixing noticeably heats up the material more than the other options, reaching up to 40C as observed immediately after removing the material, based on two-minute mixing at 2,000 RPM (as recommend by Thinky). Mixing by hand or through static mixing nozzles did not noticeably heat the material during testing. Preventing material from heating is desirable to prevent premature curing of the silicone.
The results of this test show that more mixer elements do not necessarily outperform lower-mixing element mixers with respect to the resulting material strength. For example, materials mixed with the 41 element Optimixer exhibit similar or slightly reduced tensile strength as materials mixed with the 25 element Optimixer. In addition, the former costs 70% more and retains 50% more dead volume. The larger element width of the Turbo mixers allow much higher flow rates which could be compelling to fill molds faster and with less pressure drop through the mixing element.
In our investigation of mixing efficacy using a centrifugal planetary mixer, hand mixing, and static mixing nozzles, we have found static mixing nozzles can equal or outperform all other options with regards to the resulting material tensile strength. While there are certainly static mixing nozzles that have superior performance, only one or two types of static mixing nozzles would be needed for most silicones found in a lab, and we recommend the Optimixer 25 (for cost and mix quality) and the Turbo 0.4x20 (for highest flow rate and mix quality).
All mixing methods are nearly equivalent

Silicone mixing tensile test results, for a centrifugal planetary mixer (Thinky ARE-310) and six static mixing nozzles, following ASTM D412 -- Tensile testing of Elastomers with n = 5. Ecoflex 00-30 (00-30 hardness, 3,000 cps), True Skin 30 (30A hardness, 15,000 cps), and Smooth-Sil 945 (45A hardness, 30,00 cps) were tested. Error bars represent one standard deviation.
How to Fill Nordson EFD Cartridges
The video to the left demonstrates how to fill the Nordson EFD cartridges by hand. We have designed some 3D printable cartridge holders that allow you to hold them upright while pouring and degassing.